Fixed installation for excavators with FOPS
Foreword
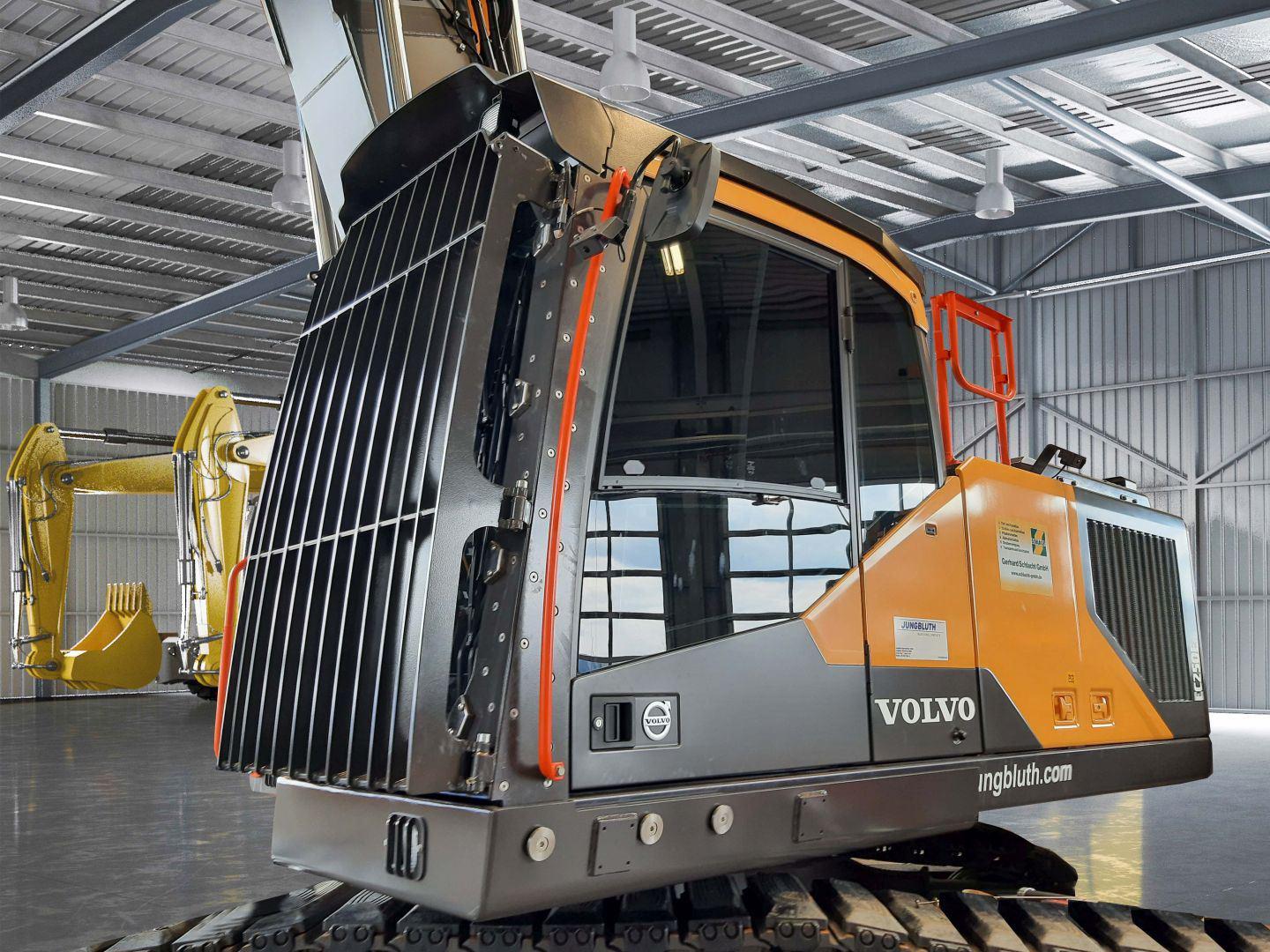
After the requests for armouring with simultaneous FOPS protection have constantly increased, we have decided to be able to offer a solution for this segment as well.
From the very beginning, it was clear to us that the safety standard for this construction also had to be redefined. If you consider that the same test conditions of the FOPS test are applied from the mini-excavator to the 100 t excavator, you quickly realise that especially for excavators from 25 t upwards, the required protection in terms of armouring is underdimensioned in relation to the dead weight and the test loads. With the increasing dead weight of the machine, not only the loads that the excavator is capable of lifting increase, but also the possible working height. The resulting possible loads on the protective equipment in the event of an accident are multiplied. For example, if the weight doubles, the impact energy doubles linearly. However, if the same weight falls on the protective equipment from a greater height, the resulting higher speed has an exponential effect on the load on the protective equipment.
Conventional FOPS concepts are predominantly mounted on the bolting points provided by the manufacturer directly on the cabin. This method of attachment means that no matter how stable the chosen FOPS construction is built beyond the FOPS requirement, the cabin construction itself always remains the weakest link.
In practice, in the event of an accident, the object usually falls on the front upper area of the cabin or it is hit directly from the front. In both cases, the cabin is stressed at its weakest point, as the A-pillars are usually slightly curved and quite delicate, especially as the skylight is usually located in the front roof area. Furthermore, HARDOX sheet metal is often used in the construction of FOPS protective equipment. This choice of material has the consequence that on the one hand it is possible to use thinner and thus lighter sheets with the same required strength. On the other hand, however, Hardox sheets have the property of hardly deforming under load, so that hardly any energy could be dissipated by deformation processes of the protective equipment. In these cases, the occurring energy is almost completely transferred to the cabin.
It should also be noted that the cabin bearings cannot be overloaded indefinitely. The dimensioning of the cabin bearings is only designed for the retrofitting of a FOPS roof with front grille and thus already brings the bearing to its load limit. It can be assumed that the additional installation of armoured glazing will lead to an overload of the bearing, which will have a negative effect in the form of shortened service life and altered damping behaviour. In the worst case, the CE requirements can no longer be met.
In principle, however, the combination of armour and front grille is desirable in demolition, as the armoured glass effectively retains almost all objects that could not otherwise be safely retained by the front grille, such as pipes or other profiles with a small frontal area but large kinetic energy.
See now what constructive solutions we have developed to significantly increase safety for the driver.
Armoured glass combined with FOPS roof and front guard
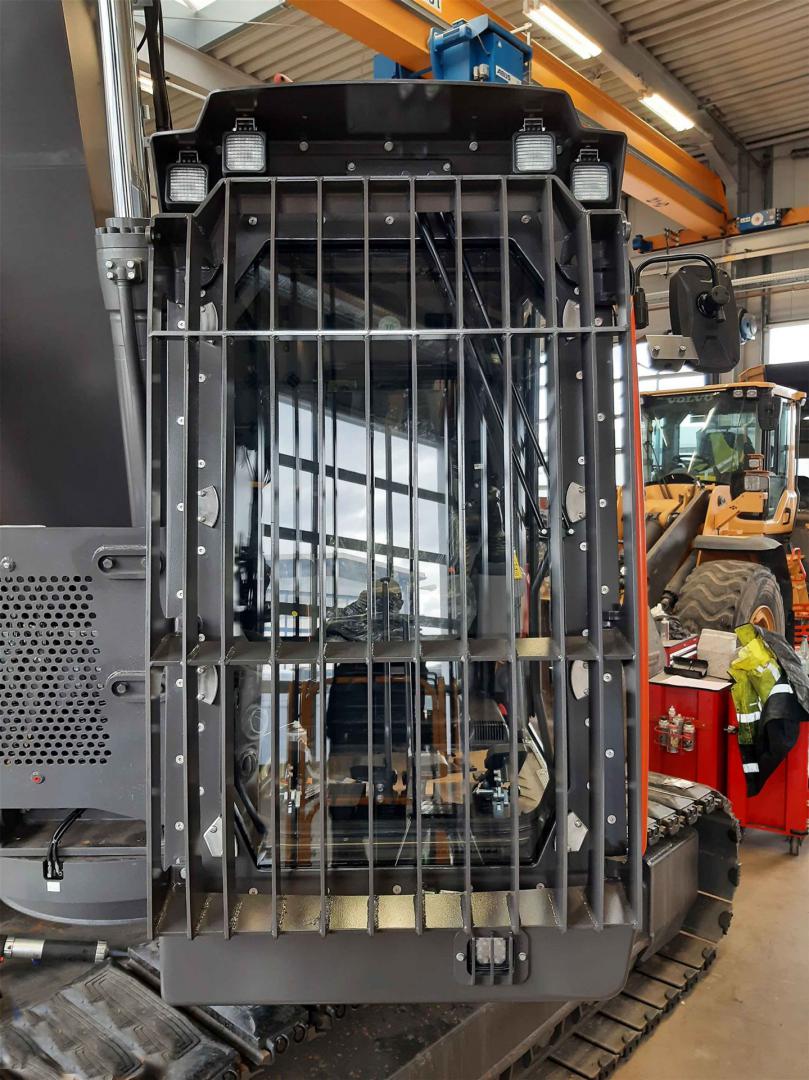
The armouring is suitable for excavators from approx. 16t and is supplied with integrated FOPS roof and front guard.
The protective conversion complies with bullet protection class BR6 NS and explosion class ER 4 as well as at least FOPS II.
Here you can see the conversion of a Volvo excavator.
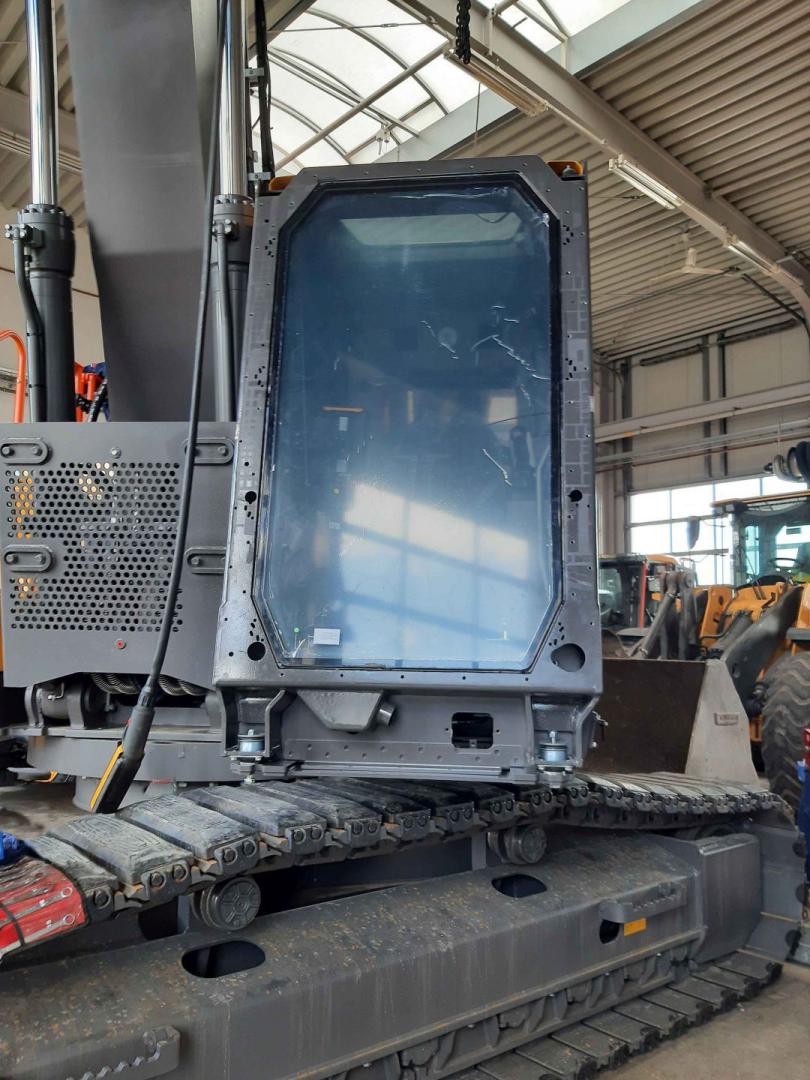
The next step is to place the armour with its weight on the base plate with the help of cone bearings and only then to screw and glue it to the cabin.
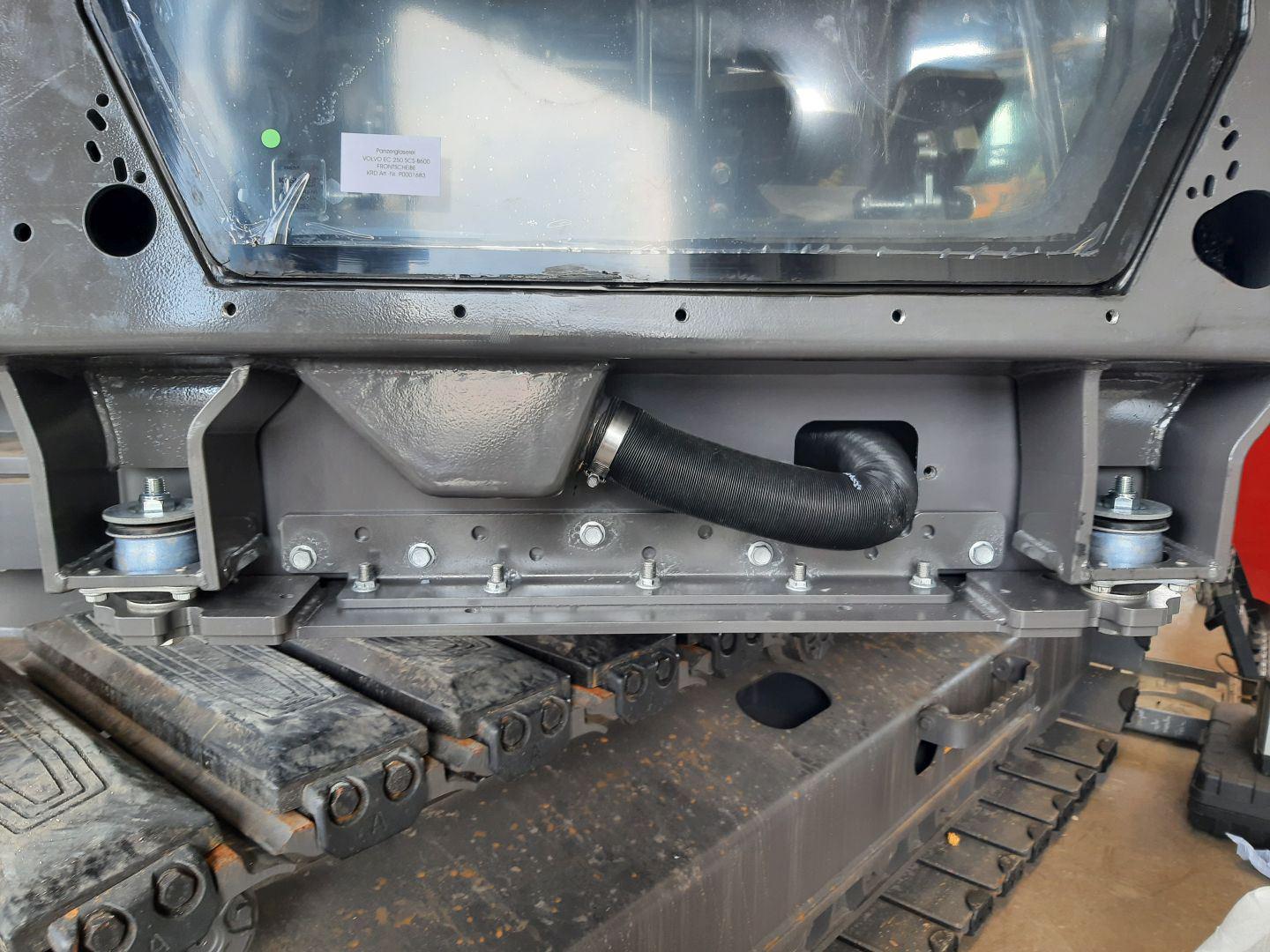
The conical bearings increase explosion protection because they prevent the cabin from tearing off in the event of an explosion. In addition, they ensure that the original cabin bearings are not overloaded and that the damping behaviour of the cabin is not negatively influenced. In the event of an accident, together with the special connecting elements, they transfer forces past the cabin into the floor assembly.
The warm air feed for the windscreen heater is clearly visible.
Assembly of the FOPS roof
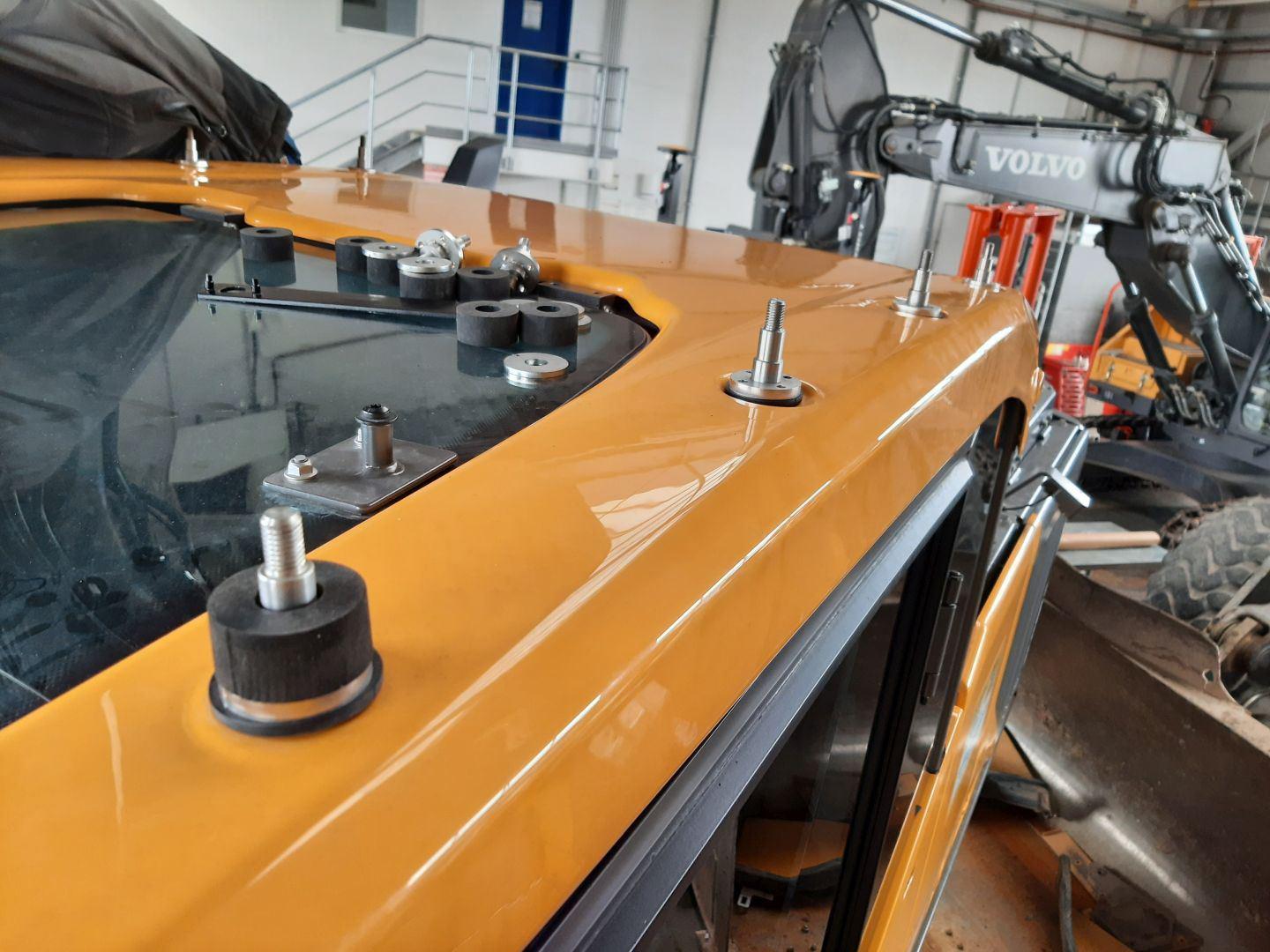
Before the FOPS roof is mounted on the cabin, the existing screws of the plastic roof skin are replaced by special fastening elements. These have the task of ensuring even load distribution through the use of polymer buffers and of dissipating energy in the event of damage.
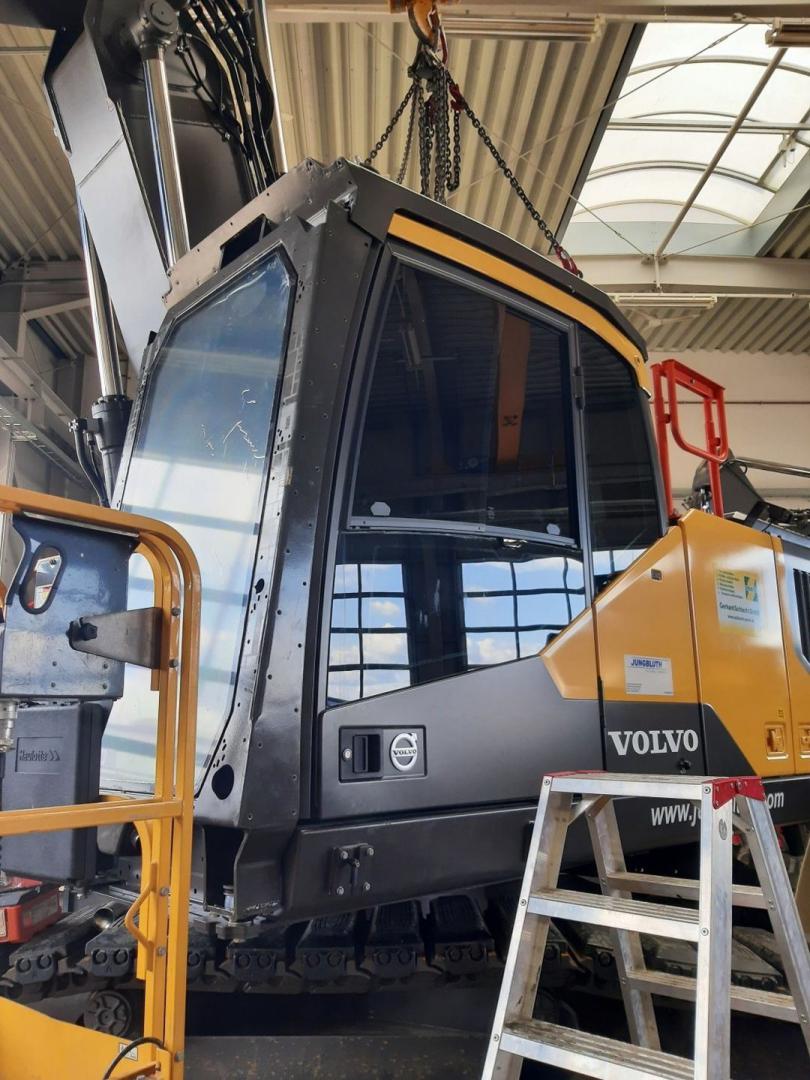
Now the FOPS roof can be placed on its attachment points. We have included the armour in the structural analysis of the FOPS roof, as it is attached to the armour in the front area. With these measures, the roof, armour and floor assembly become one unit and can thus safely dissipate large forces around the cabin into the floor assembly. The massive box frame of the armour can absorb forces from above as well as from the front and the side like a front roll bar.
Special fasteners
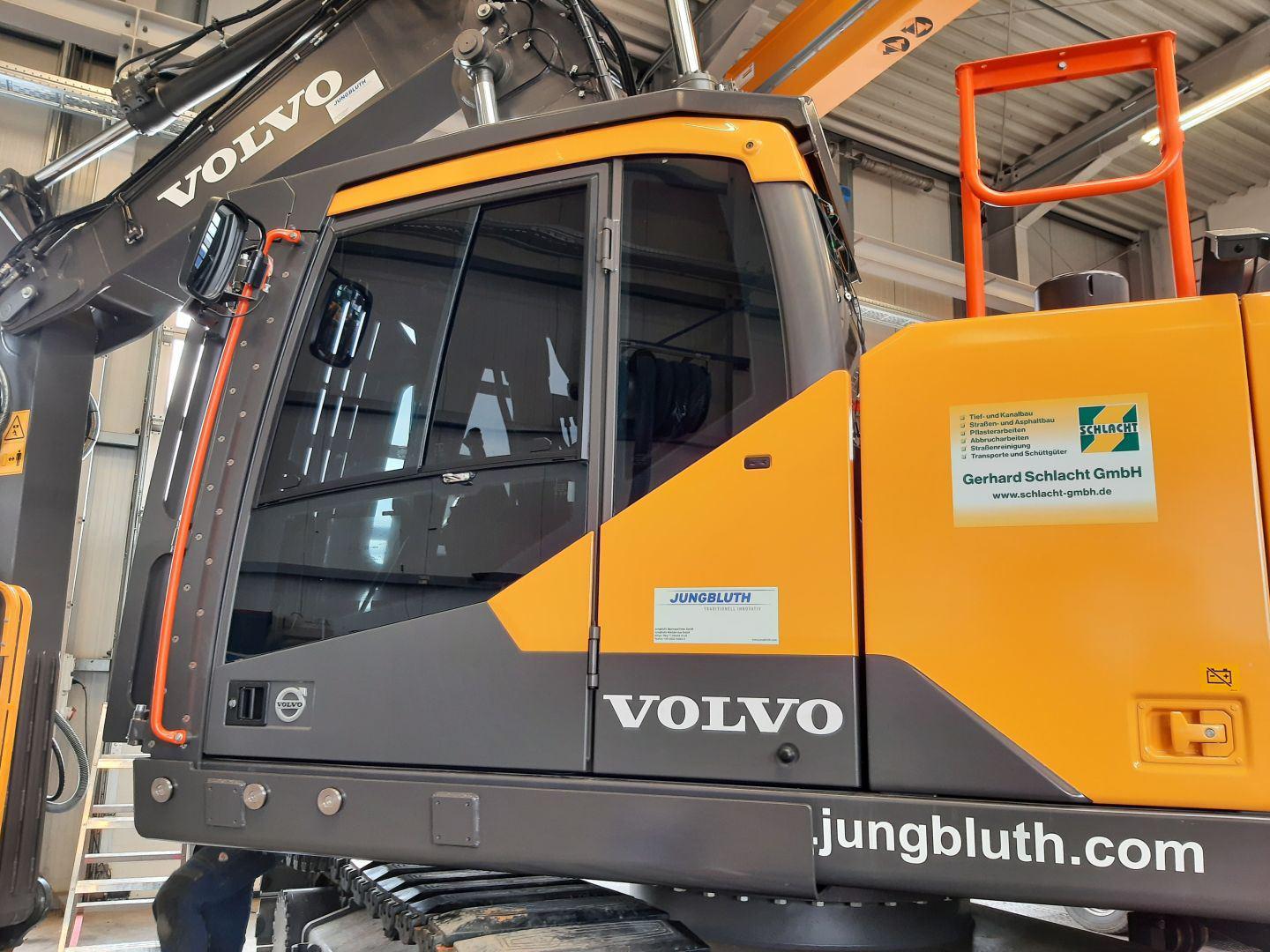
After all the other parts have been assembled, it is easy to see that additional metal sheets have been attached to the sides of the frame, which are elastically connected to the floor pan with special connecting elements. These plates form a triangle between the floor pan and the windshield frame and further stiffen the entire construction. This makes the armouring even more resistant to loads from the front and for FOPS safety, for loads that strike at an angle from above.
Additional protection against splinter throw
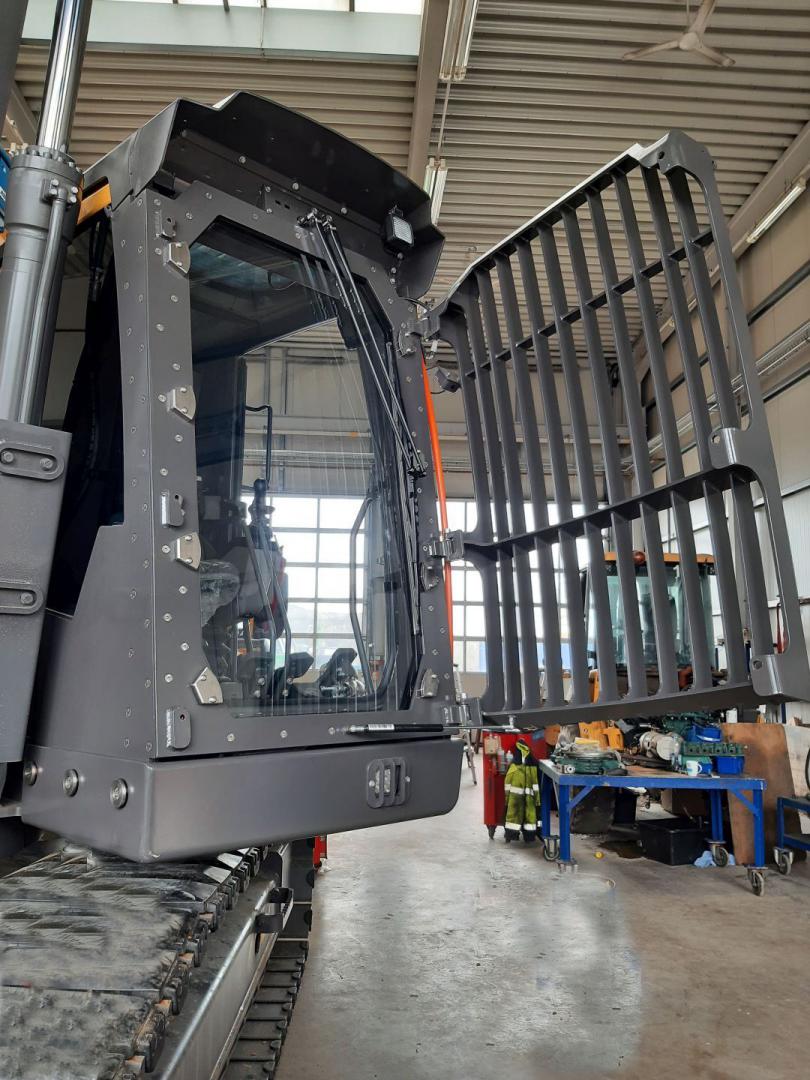
The side panel on the right-hand side is raised up to the lower edge of the side window and, together with the raised floor pan on the side, provides additional protection for the driver against splinters.
The outer hot-air nozzles and the sturdy front grille, which is held open by a gas pressure spring, are clearly visible.
The screwed-on 8mm cover plate serves as a mounting platform for the front grille and the hot air nozzles, but also has the task of covering and protecting the lateral edge of the windshield, since bullet-proof windshields in the edge area do not have the full bullet performance as in the surface area.
Stable roof structure
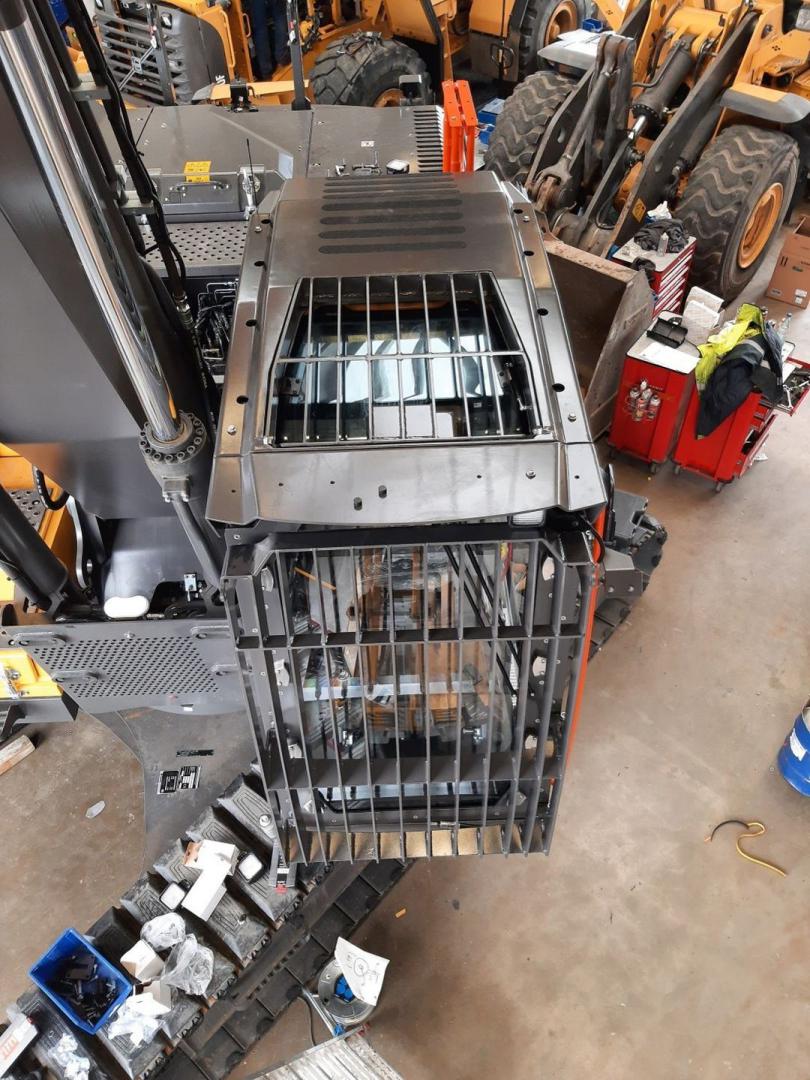
The stable roof structure with integrated roof grille and bolted-on weather protection roof is clearly visible. This can accommodate up to six worklights and can be replaced if damaged. If desired, the weather protection roof can also be equipped with only two worklights on the right and left, but with a light bar in the middle.
Special design features
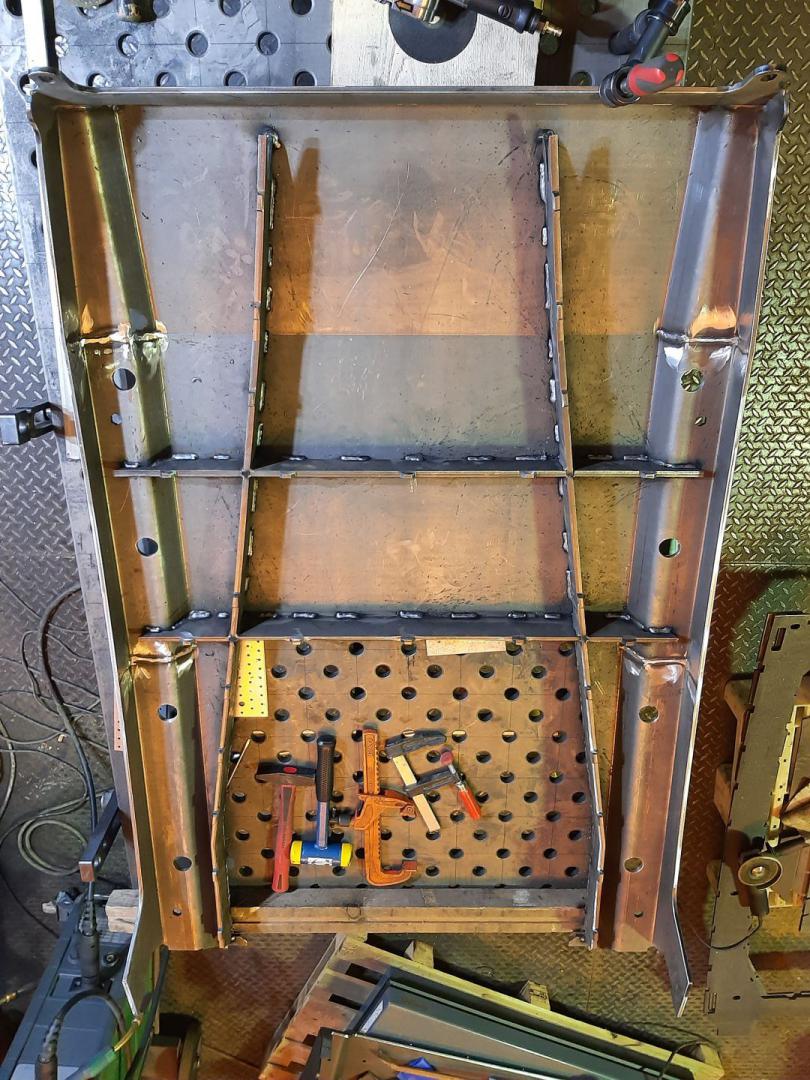
The FOPS roof is made of 8mm folded steel, grade 235 to 355. The stiffeners are made of 10mm steel. An 8mm inner sheet is later welded onto this reinforcement. By using unhardened steel, the roof can still deform to dissipate energy and, with a thickness of 8mm, still has enough dielectric strength.
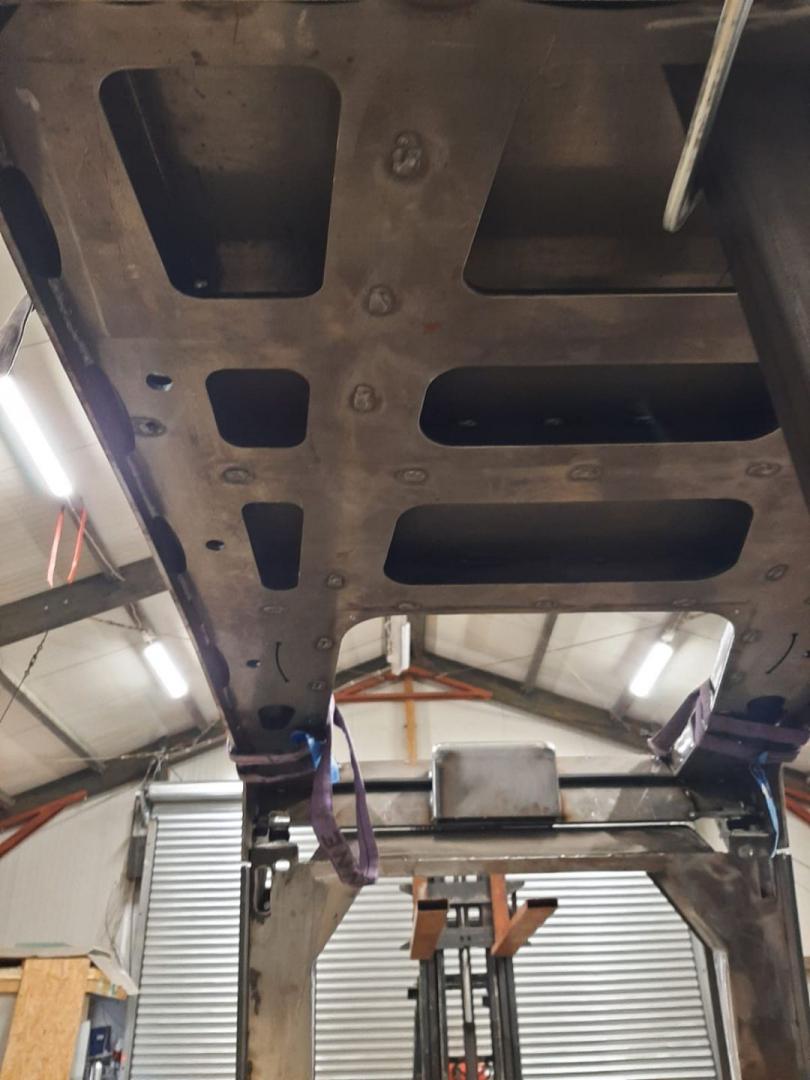
The 8mm inner plate is clearly visible. Due to the arrangement of the weld seams and the free cut in the front area, the inner sheet can still deform under very heavy load in order to destroy energy.
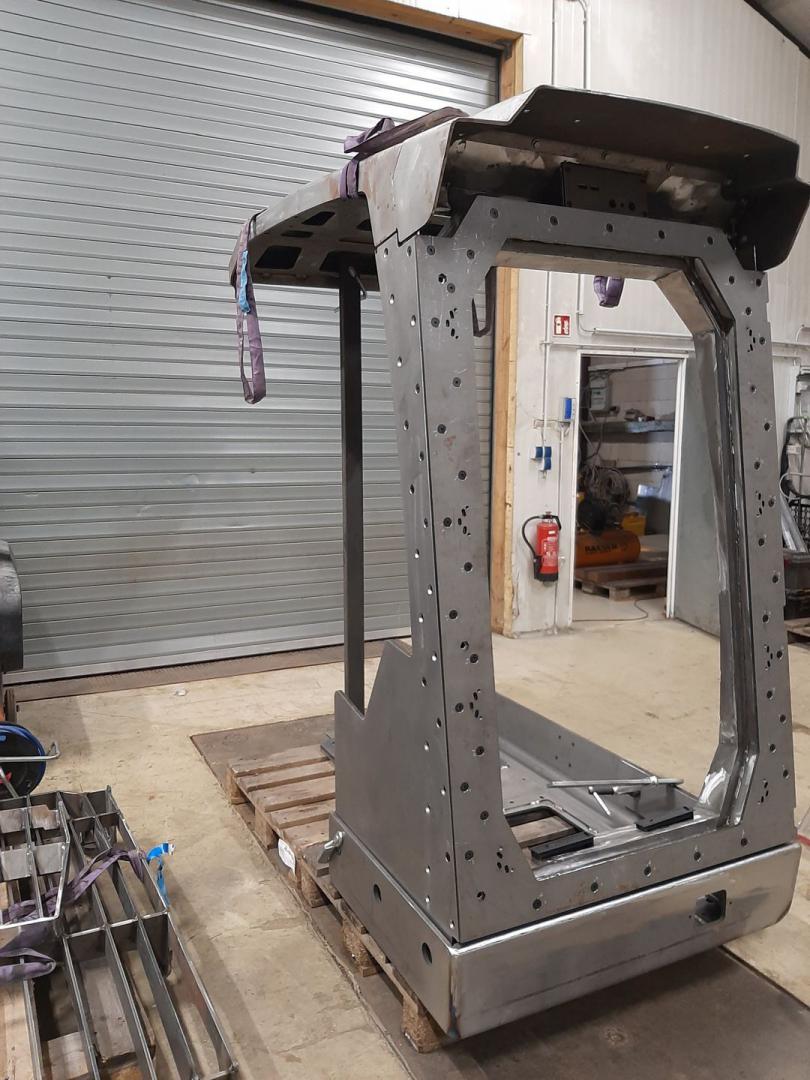
This type of armouring in combination with the FOPS roof is a self-supporting structure built around the driver's cabin. While it also utilises the inherent stability of the cab and the FOPS roof also transfers forces to the stable rear area in the event of an accident, the numerous features we have described above ensure that the cab structure remains intact as long as possible to effectively protect the driver.
Options in detail
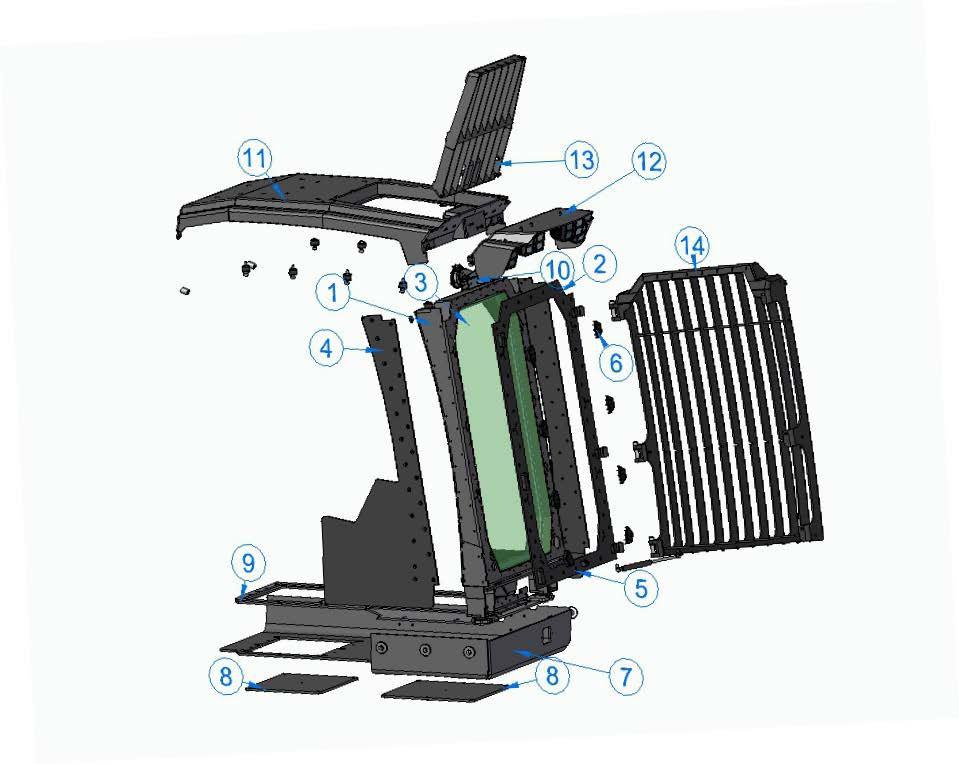
1. fixed installation frame in accordance with the latest DGUV with bullet protection class BR 6 S / NS and explosion class ER 4 in conjunction with FOPS roof and front guard in accordance with FOPS 2. The base frame is made of 8 mm sheet steel, which forms a torsion-resistant box profile. The weight of the armour is transferred to the floor assembly via conical bearings as standard and additionally connected to the side of the floor pan with six special fastening elements. At the rear, the frame is bolted and glued to the cabin.
2. 8mm steel pane cover, screwed to the frame, prepared for mounting a front grille O.A. 8mm steel pane cover , screwed to the frame.
3. surcharge for polycarbonate pane BR 6 NS from the company Kasiglass
4. lateral reinforcement plate on the right made of 12mm steel plate
5. lateral reinforcement plate on the left made of 12mm steel plate
6. windscreen heating kit consisting of eight stainless steel nozzles on the outside and two plastic nozzles on the inside as well as the inner air duct. (Cannot be retrofitted) Warm air generation via external parking heater 7,8,9. Floor assembly with screwable inspection hatches edged high on the sides.
10. wiper module 24V
11. FOPS roof Heavy-duty version, roof skin and lower sheet made of 8mm sheet steel. Inner bracing of 10 mm steel sheet.
12. screwed weather protection roof made of 8mm sheet steel for six spotlights
13. protective grille on top. Hinged version with gas pressure damper heavy-duty version. Made of 8 mm and 10 mm sheet steel.
14. front grille hinged on, heavy-duty version, with gas pressure damper
15.O.A.Elekto attachment kit for wiper module (Must be connected by an electrician)
16. o.a. Adjustable wiper arms
17. O.A. Wiper Blade 1000mm
Armoured glass combined with FOPS roof and front guard
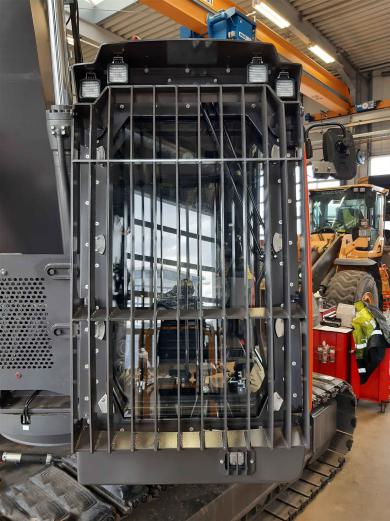
The armouring is suitable for excavators from approx. 16t and is supplied with integrated FOPS roof and front guard.
The protective conversion complies with bullet protection class BR6 NS and explosion class ER 4 as well as at least FOPS II.
Here you can see the conversion of a Volvo excavator.
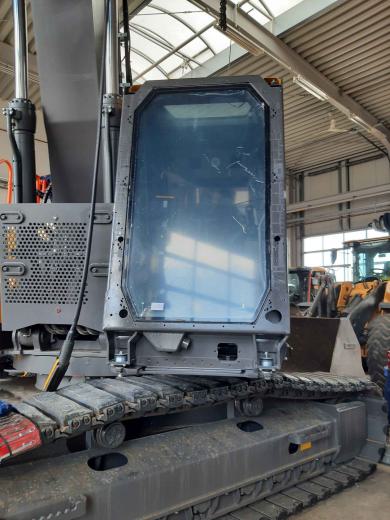
The next step is to place the armour with its weight on the base plate with the help of cone bearings and only then to screw and glue it to the cabin.
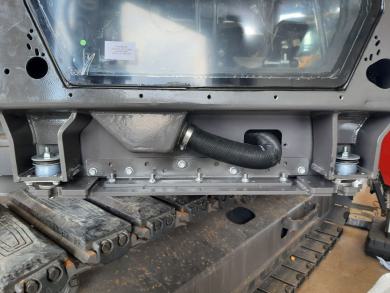
The conical bearings increase explosion protection because they prevent the cabin from tearing off in the event of an explosion. In addition, they ensure that the original cabin bearings are not overloaded and that the damping behaviour of the cabin is not negatively influenced. In the event of an accident, together with the special connecting elements, they transfer forces past the cabin into the floor assembly.
The warm air feed for the windscreen heater is clearly visible.
Special design features
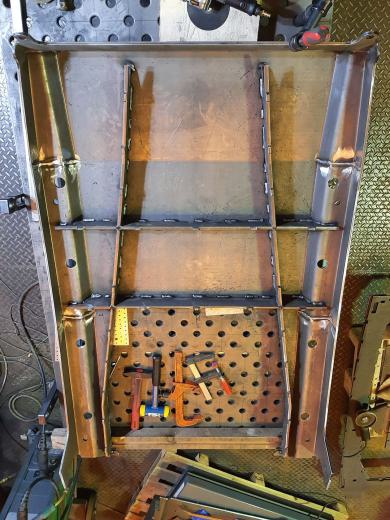
The FOPS roof is made of 8mm folded steel, grade 235 to 355. The stiffeners are made of 10mm steel. An 8mm inner sheet is later welded onto this reinforcement. By using unhardened steel, the roof can still deform to dissipate energy and, with a thickness of 8mm, still has enough dielectric strength.

The 8mm inner plate is clearly visible. Due to the arrangement of the weld seams and the free cut in the front area, the inner sheet can still deform under very heavy load in order to destroy energy.
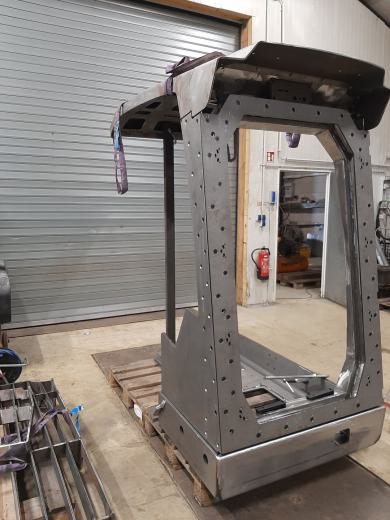
This type of armouring in combination with the FOPS roof is a self-supporting structure built around the driver's cabin. While it also utilises the inherent stability of the cab and the FOPS roof also transfers forces to the stable rear area in the event of an accident, the numerous features we have described above ensure that the cab structure remains intact as long as possible to effectively protect the driver.
Assembly of the FOPS roof
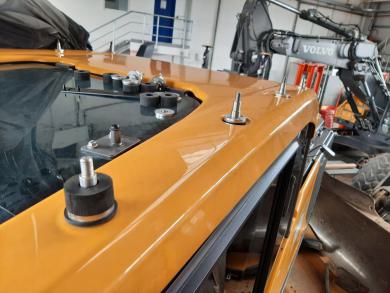
Before the FOPS roof is mounted on the cabin, the existing screws of the plastic roof skin are replaced by special fastening elements. These have the task of ensuring even load distribution through the use of polymer buffers and of dissipating energy in the event of damage.
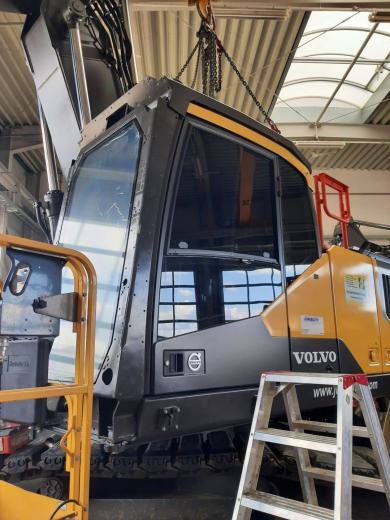
Now the FOPS roof can be placed on its attachment points. We have included the armour in the structural analysis of the FOPS roof, as it is attached to the armour in the front area. With these measures, the roof, armour and floor assembly become one unit and can thus safely dissipate large forces around the cabin into the floor assembly. The massive box frame of the armour can absorb forces from above as well as from the front and the side like a front roll bar.
Special fasteners
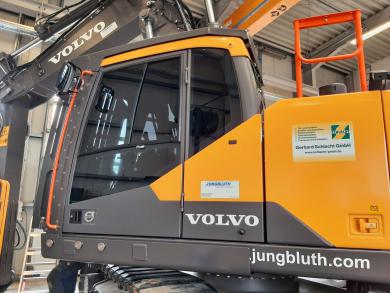
After all the other parts have been assembled, it is easy to see that additional metal sheets have been attached to the sides of the frame, which are elastically connected to the floor pan with special connecting elements. These plates form a triangle between the floor pan and the windshield frame and further stiffen the entire construction. This makes the armouring even more resistant to loads from the front and for FOPS safety, for loads that strike at an angle from above.
Additional protection against splinter throw
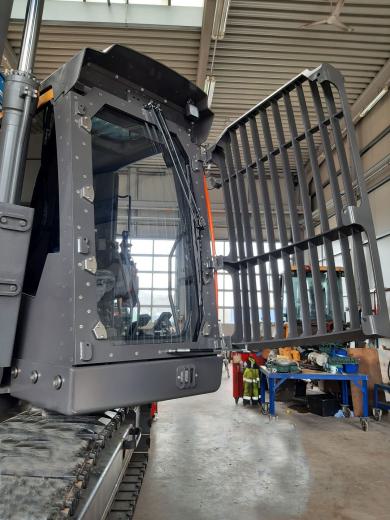
The side panel on the right-hand side is raised up to the lower edge of the side window and, together with the raised floor pan on the side, provides additional protection for the driver against splinters.
The outer hot-air nozzles and the sturdy front grille, which is held open by a gas pressure spring, are clearly visible.
The screwed-on 8mm cover plate serves as a mounting platform for the front grille and the hot air nozzles, but also has the task of covering and protecting the lateral edge of the windshield, since bullet-proof windshields in the edge area do not have the full bullet performance as in the surface area.
Stable roof structure
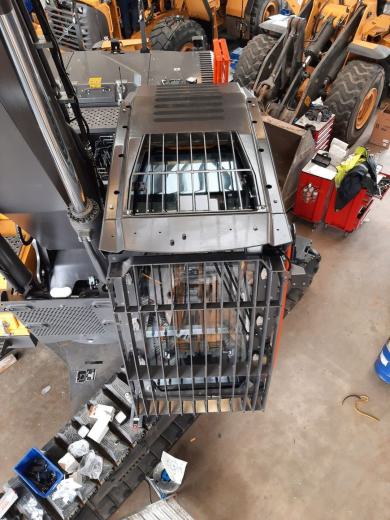
The stable roof structure with integrated roof grille and bolted-on weather protection roof is clearly visible. This can accommodate up to six worklights and can be replaced if damaged. If desired, the weather protection roof can also be equipped with only two worklights on the right and left, but with a light bar in the middle.
Options in detail
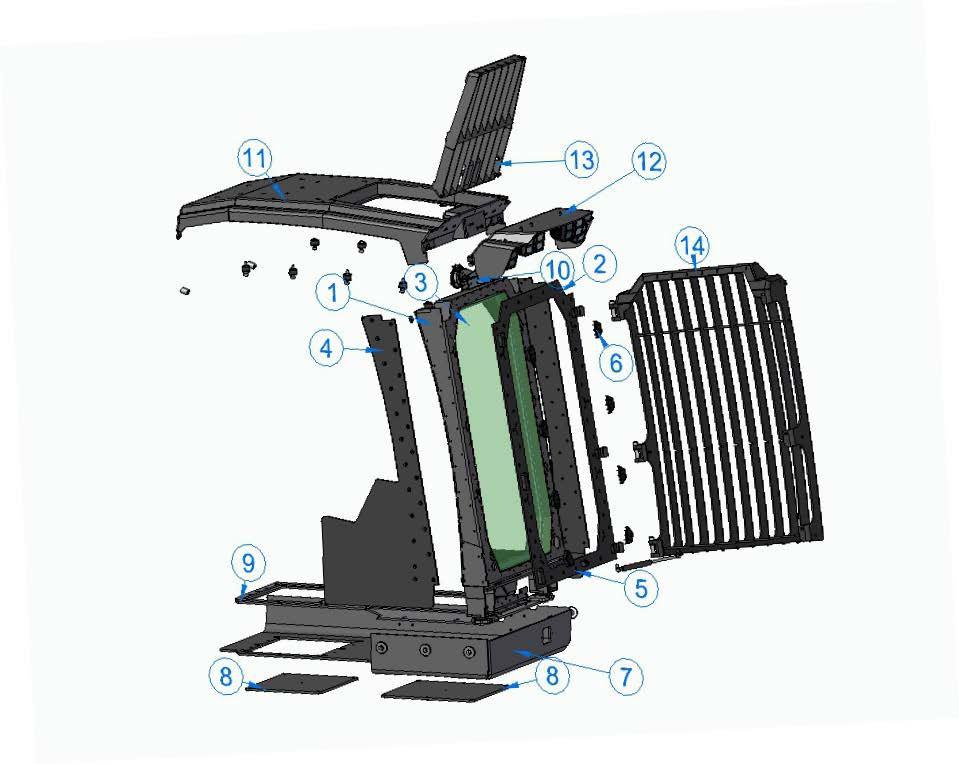
1. fixed installation frame in accordance with the latest DGUV with bullet protection class BR 6 S / NS and explosion class ER 4 in conjunction with FOPS roof and front guard in accordance with FOPS 2. The base frame is made of 8 mm sheet steel, which forms a torsion-resistant box profile. The weight of the armour is transferred to the floor assembly via conical bearings as standard and additionally connected to the side of the floor pan with six special fastening elements. At the rear, the frame is bolted and glued to the cabin.
2. 8mm steel pane cover, screwed to the frame, prepared for mounting a front grille O.A. 8mm steel pane cover , screwed to the frame.
3. surcharge for polycarbonate pane BR 6 NS from the company Kasiglass
4. lateral reinforcement plate on the right made of 12mm steel plate
5. lateral reinforcement plate on the left made of 12mm steel plate
6. windscreen heating kit consists of eight stainless steel nozzles on the outside and two nozzles made of plastic on the inside, as well as the inner air duct. ( Cannot be retrofitted) Warm air generation via external parking heater 7,8,9. Floor assembly with screwable inspection hatches edged high on the sides.
10. wiper module 24V
11. FOPS roof heavy-duty version, roof skin and bottom sheet made of 8mm sheet steel. Inner bracing of 10 mm sheet steel.
12. screwed weather protection roof made of 8mm sheet steel for six spotlights
13. protective grille on top. Hinged version with gas pressure damper heavy-duty version. Made of 8 mm and 10 mm sheet steel.
14. front grille hinged on, heavy-duty version, with gas pressure damper
15.O.A. Electrical attachment kit for wiper module (Must be connected by an electrician)
16. o.a. Adjustable wiper arms
17. O.A. Wiper Blade 1000mm